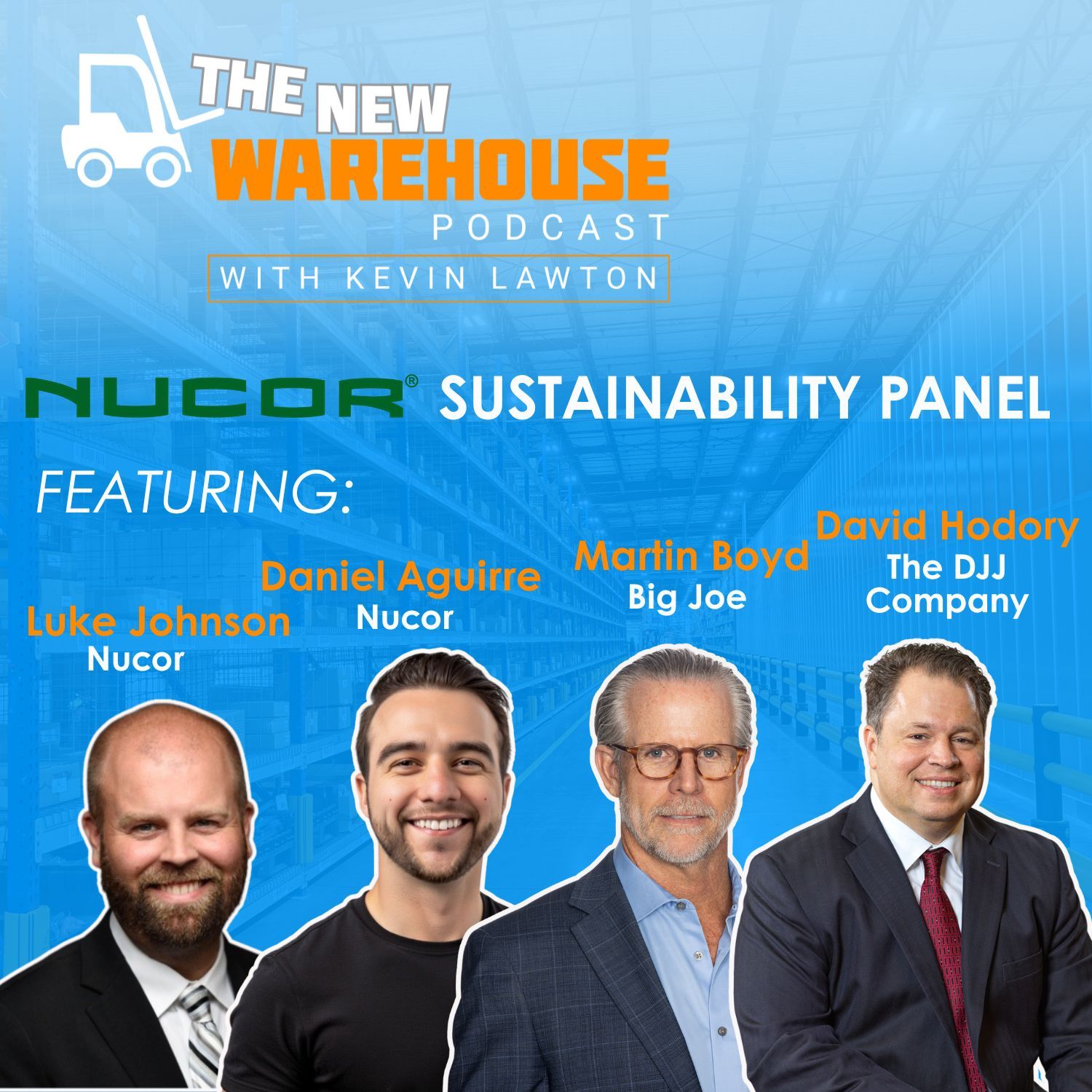
579: The Journey to Sustainable Warehousing, Insights from ProMat 2025
Welcome to this special panel episode of The New Warehouse Podcast, recorded live at ProMat 2025 in Chicago. In this episode, host Kevin moderates a conversation with leaders from Nucor, Big Joe Forklifts, and David J. Joseph Company (DJJ) to explore the evolving role of sustainability in the warehouse and the material-handling industry. Panelists include Luke Johnson, Sustainability Supervisor at Nucor; Daniel Aguirre, Commercial Director at Nucor’s Warehouse Division; Martin Boyd, Chief Marketing Officer at Big Joe Forklifts; and David Hodory, Marketing Manager at DJJ. The discussion dives into modern steelmaking, innovative racking systems, warehouse electrification, and how companies can implement practical and measurable sustainability goals today.
Steelmaking Innovation: A Greener Foundation for Sustainable Warehousing
Luke Johnson from Nucor opened the panel by distinguishing between two steelmaking processes: the traditional blast furnace and the electric arc furnace (EAF) method. While blast furnaces use virgin materials and fossil fuels, Nucor’s EAF technology melts recycled steel using electricity—cutting greenhouse gas emissions by two-thirds.
“Nucor owns and operates 25 mills… All 25 of our mills utilize that EAF technology to make steel.”
In 2023, Nucor’s steel had 77% recycled content—a metric expected to increase as they push new technologies. The upcoming mill in Lexington, North Carolina, will feature AI-powered energy monitoring and nine integrated robots for process automation.
David Hodory from DJJ, a Nucor subsidiary, emphasized that steel is endlessly recyclable. He shared how DJJ handles over 20 million tons of scrap annually and is now even mining landfills in Florida for aluminum and copper.
“There are plenty of opportunities in the space to continue to refine the recycling and sortation process… which from a carbon and landfill perspective is really impactful.”
Retrofitting Warehouses with Circular Design in Mind
Daniel Aguirre spotlighted the importance of aligning warehouse infrastructure with long-term growth, automation, and environmental goals.
“The biggest challenge that we see with our customers is understanding their growth… and how do you incorporate that within your design and engineering?”
Their team’s innovative product, Tube Rack, improves seismic performance and allows for modular replacement—reducing waste and enhancing lifecycle management. Nucor and DJJ also support full circularity by reclaiming old racking systems, turning them into new raw material, and then redistributing them to customers.
Martin Boyd of Big Joe Forklifts added that switching from internal combustion forklifts to lithium-powered units is key to decarbonizing operations:
“Our primary goal is to move companies… from internal combustion to electric.”
This transformation requires upfront planning, including evaluating warehouse electrical infrastructure and optimizing charger placement. But the payoffs—in energy efficiency and sustainability—are substantial.
Tackling Barriers and Driving Adoption Through Partnerships
Despite the benefits of sustainable technologies, the transition can feel overwhelming. According to Marty, the key is education and demonstration.
“We really find that it’s important that we not only partner with our dealer partners but also with the end users… to make them feel that they’re not in this alone.”
Big Joe’s “Demo, Demo, Demo” approach helps alleviate fears and provides real-world performance data via telemetry. For Daniel, partnerships also mean supporting customers with transparent metrics like Environmental Product Declarations (EPDs) and sourcing documentation.
On a broader level, Luke discussed how Nucor is backing scalable carbon-reduction technologies. These include carbon capture systems (with ExxonMobil), renewable energy investments, and even small modular nuclear reactors.
“We do believe that nuclear plays a role… to fully decarbonize, we need that baseline source of reliable power.”
Key Takeaways on Sustainable Warehousing
- Nucor’s steelmaking uses 77% recycled content and EAF technology that emits 1/3 of the carbon footprint of traditional methods.
- DJJ processes 20M+ tons of scrap annually, pioneering landfill mining to recover metals.
- Big Joe’s lithium forklifts replace internal combustion units and reduce operator downtime and emissions.
- Nucor invests in carbon capture, renewable energy projects, and SMRs for deep decarbonization.
- Tube Rack systems allow modular replacement, minimizing waste in retrofits.
- Customers are encouraged to source domestically, demand transparency, and demo new technologies to overcome fear and inertia.
Recyclability, efficient logistics, and closed-loop systems can create measurable warehouse sustainability gains across the supply chain.
Listen to the episode below and leave your thoughts in the comments.
Guest Information
Nucor Corporation: nucor.com
Big Joe Forklifts: bigjoeforklifts.com
The David J. Joseph Company (DJJ): djj.com
Luke Johnson on LinkedIn, click here.
Daniel Aguirre on LinkedIn, click here.
Martin Boyd on LinkedIn, click here.
David Hodory on LinkedIn, click here.
For more information about sustainable warehousing, check out the podcasts below.
536: Paving the Way to Warehouse Sustainability with Green Building Initiative
Sustainability in the Warehouse Industry: Strategies and Challenges