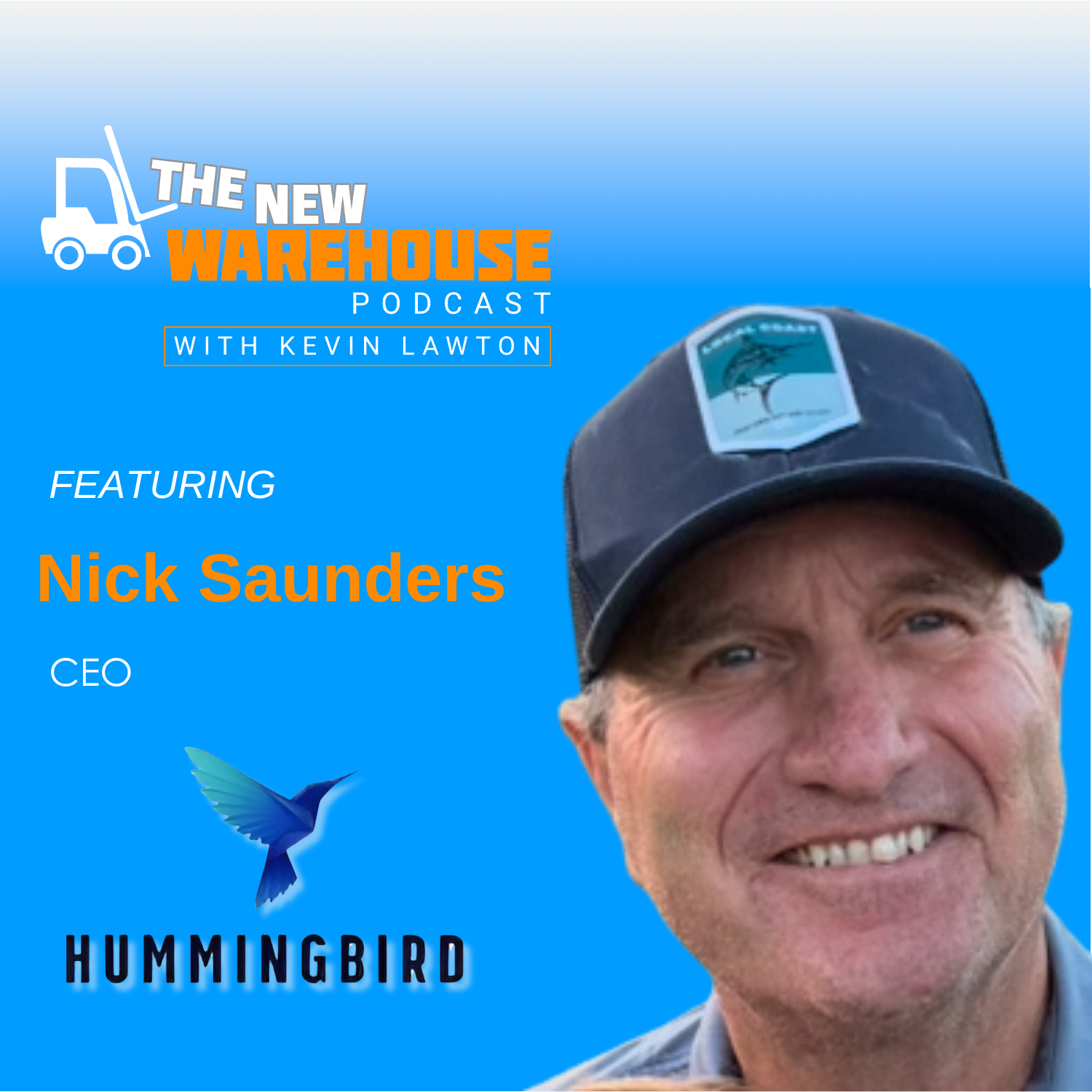
556: Warehouse Picking with Drone Technology
In this episode of The New Warehouse Podcast, Nick Saunders, CEO and co-founder of Hummingbird Systems, discusses a groundbreaking approach to warehouse picking. With a rich history in logistics and automation, Saunders and his team are leveraging drones to address two significant warehouse challenges: labor shortages and real estate costs. Hummingbird Systems stands out with a tethered drone solution that redefines how warehouses utilize vertical space and tackle operational inefficiencies. Saunders’ journey is one of solving real-world problems with practical solutions.
Addressing Warehouse Pain Points with Drone Technology
Labor and real estate remain two of the biggest cost centers in warehousing. “The quality of available labor has been steadily declining, and the costs are increasing, especially during peak seasons,” Saunders explained. The tethered drones developed by Hummingbird Systems address these pain points by enabling continuous picking operations while maximizing vertical storage. Saunders adds, “You’re already paying for the square footage the racking sits on. Now, you’re unlocking all that vertical storage space that can become a fast-moving pick location that you otherwise underutilized.” The tether system offsets drone weight, ensuring an uninterrupted eight-hour shift with minimal operational disruptions. This approach optimizes existing warehouse footprints and increases throughput during high-demand periods.
Tethered vs. Free-Flying Drones
While many companies utilize drones for inventory counting, Hummingbird Systems is taking a different path. “Inventory is important, but it’s just a feature, not a business,” Saunders stated. The tethered drone model allows for more efficient, precise picking. “When you tether the drone, you achieve full time-on-task picking—up to an 8-hour uninterrupted shift. The tether and spring-loaded trolley system offset 7 to 10 pounds of the drone’s weight and payload while enabling multi-agent collision avoidance.” Hummingbird drones can work collaboratively within existing workflows by combining tethering with advanced multi-agent collision avoidance. This system unlocks the potential of underutilized vertical storage space, transforming it into high-speed picking zones. “We aim to solve the discrete item pick challenge at a low cost while keeping it simple,” Saunders noted.
Painting a Vision for Collaborative Automation with Drone Technology
Saunders envisions a warehouse ecosystem where tethered drones seamlessly integrate with Autonomous Mobile Robots (AMRs). “You look down an aisle, and the drones are tethered, picking items and dropping them into AMRs, transporting them to packing stations,” he explained. This eliminates human intervention in picking and transport, significantly boosting operational efficiency. Starting with apparel, accessories, and nutraceuticals, Hummingbird’s solution is tailored for items under five pounds, which account for 85–90% of e-commerce shipments. With pilot programs already in progress, Saunders believes the technology will soon redefine warehouse automation.
Key Takeaways
- Hummingbird’s tethered drones enable uninterrupted picking shifts and optimize vertical storage.
- Their approach addresses labor shortages and rising costs during peak seasons.
- The system focuses on lightweight items, aligning with e-commerce demands.
Listen to the episode below and leave your thoughts in the comments.
Guest Information
For more information on Hummingbird Systems, click here.
To connect with Nick on LinkedIn, click here or email him at nsaunders@hbird.tech.
For more information about drone technology and how it’s impacting warehouses, check out the content below.
Navigating the Future: Robotics in Supply Chain and Warehousing